How Namuda Enhances the Value of Lean Six Sigma through the DMAIC phases
Lean Six Sigma is a methodology for improving efficiency, reducing waste and ensuring quality in business processes. It combines the process improvement methods of Six Sigma and Lean enterprise and helps to establish a clear path to achieving improvement objectives. However, traditional Lean Six Sigma relies heavily on manual data collection,workshops, and subjective assessments, which can slow down decision-making and limit insights.
This is where Namuda comes in and enhances the value of the Lean Six Sigma methodology. By utilizing the digital footprints from business process activities that are left in IT systems like ERP or CRM, Namuda provides real-time,data-driven process discovery and improvement that significantly enhance the effectiveness of Lean Six Sigma initiatives. In this post, we’ll explore how Namuda strengthens each phase of DMAIC (Define, Measure, Analyze, Improve, Control)—the core structure of Lean Six Sigma.
1. Define – Setting business goals
The first step in Lean Six Sigma is to identify the main problems and to define goals, missions and objectives. Using Namuda we start by defining company missions and the major objectives for each of the stakeholders. Now the foundation is set for starting the improvement initiatives.
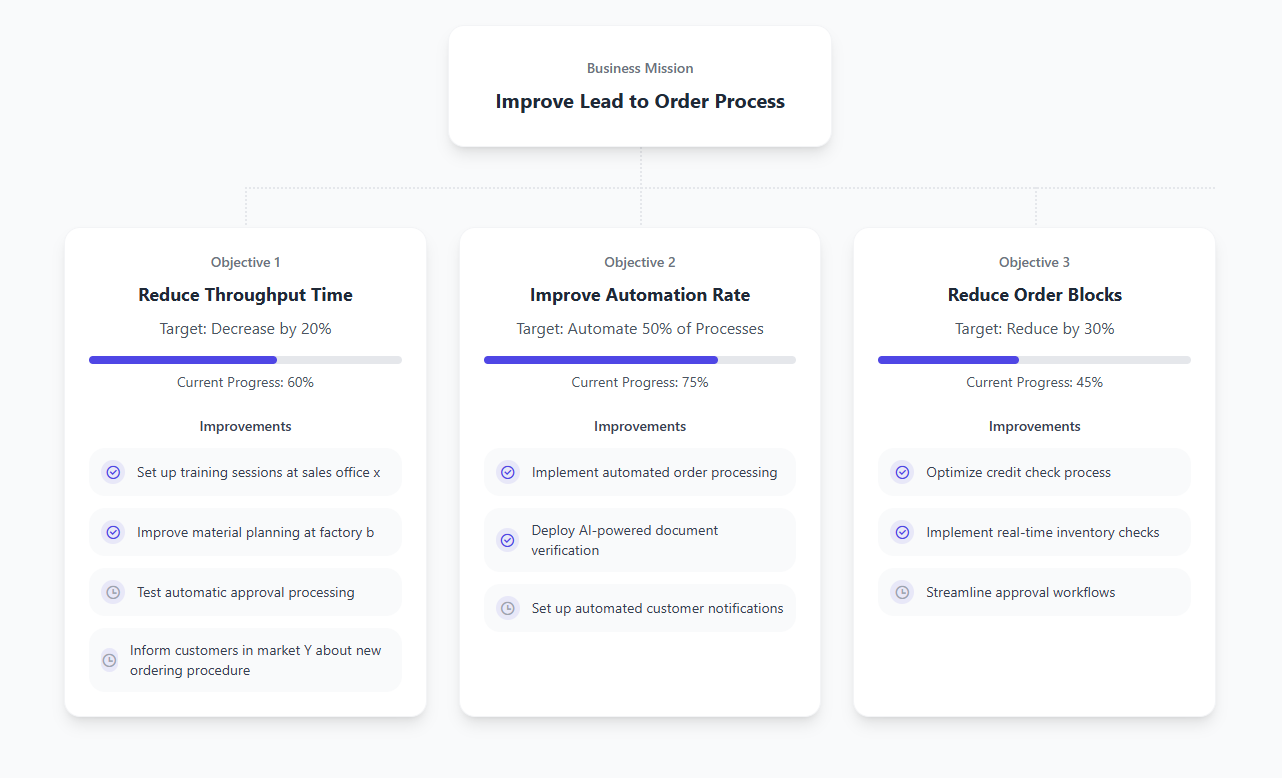
2. Measure – Replacing Guesswork with Real Data
In the "Measure" phase, Lean Six Sigma focuses on gathering data to quantify process performance. Traditionally, this involves time studies, surveys, and manual sampling—often leading to incomplete or outdated information. Namuda connects to real time data and provides updated information about your processes:
- Real-time KPIs like cycle times, rework rates, and compliance levels, or custom defined KPIs
- Mesure Data quality so that they can ensure that the data can be trusted and used in the intended way
- Tracking of process variants to see how the same process runs under different conditions
- Performance benchmarking across regions, products, or customer segments
Instead of relying on estimates, organizations can work with accurate, system-generated process data.
3. Analyze – Uncovering Root Causes with AI
Finding the root cause of inefficiencies is one of the most challenging steps in Lean Six Sigma. Traditionally, teams rely on brainstorming sessions, workshops, manual cause-and-effect diagrams, and gutfeelings.
Namuda eliminates the guesswork and helps teams focus on fixing the real causes of inefficiencies:
- AI driven findings - and recommended improvements to find patterns and rootcauses behind problems
- Detecting hidden inefficiencies with automatic bottleneck detection
- Process Canvas with digital twin of the process to be analyzed, with supporting dimensions, insights and advanced filtering capabilities
This means teams can focus on fixing the real root causes rather than relying on subjective opinions.

4. Improve – Implementing Changes with Confidence
Once the root causes and deviations are identified, Lean Six Sigma practitioners design and implement improvements. However, predicting the impact of changes is often challenging.
Namuda continuously monitors live data to track process improvements, ensuring that initiatives deliver the expected results.
With these insights, teams can make data-backed decisions, minimizing risks associated with process changes.
5. Control –Sustaining Gains with Continuous Monitoring
Sustaining improvements is one of the biggest challenges in Lean Six Sigma. Traditional methods rely on periodic audits and manual reporting, making it difficult to detect process deviations in real time.
With Namuda you get
- Real-time process monitoring to detect deviations when it actually happens
- Automated alerts when processes stray from expected performance, so that actions can be taken immediately
- Continuous compliance tracking to ensure processes stay within defined limits
With Namuda, businesses can maintain improvements and prevent inefficiencies from creeping back in —ensuring continuous operational excellence.
Why Namuda is a Game-Changer for Lean Six Sigma
Lean Six Sigma is a powerful methodology, but its effectiveness depends on accurate, timely, and comprehensive data. Namuda provides that data, transforming Lean Six Sigma from a manual, assumption-driven process into a real-time, AI-powered optimization strategy.
By integrating Namuda into your Lean Six Sigma initiatives, you can drive faster, smarter, and more sustainable process improvements—leading to higher efficiency, lower costs, and better business outcomes.
🚀 Ready to Take Your Lean Six Sigma Program to the Next Level?
At Namuda, we help organizations optimize their operations by combining the power of AI and process mining. Want to see how it works? Get in touch with us today!